Through the research on the casting process and material of the rolling plate of the medium and heavy plate cooling bed, a new method of making roulette iron castings with multiple stacks of metal resin sand cores is studied. The method has simple process, high productivity, high casting comprehensive performance and good surface quality.
Current Status Of Roulette Cast Iron Parts Casting Process
Roulette cast iron parts refer to a type of castings whose diameter is much larger than the height. Generally, the processing requirements of the intermediate shaft hole are relatively high, the hub and the rim are thicker, and the wall at the spoke is thin, which easily causes uneven temperature and large temperature difference. The hub and the rim are two hot spots. If the casting process is unreasonable, the casting is prone to shrinkage cavity, shrinkage porosity and crack defects. At present, most domestic manufacturers produce roulette castings using ordinary clay sand molding, single-piece casting, tangential gate injection, and riser feeding or casting methods used in conjunction with chilled iron at the hub. This method occupies a large space, the process yield, yield and production efficiency are low, and the surface quality of the casting is poor.
After we received the production task of roulette-type iron castings-cooling bed rollers (more than 5700 pieces), the first problem to be solved is the research of the casting process. The process is required to be simple, so that workers who are not familiar with casting can operate. It is required to reduce the molding and pouring area, and meet the production needs under the existing production conditions. When studying the casting process, we encountered material problems again. The roll plate made was very brittle and could not be used in production at all. Through the research on the casting process and material of the casting, a new type of casting process for roulette cast iron parts was researched, and qualified rollers were produced.
Main Research Contents And Key Technologies
1.Material research
Roller plate is one of the key components of cooling bed equipment. It requires good surface quality and high heat resistance. The heat resistance of cast iron depends mainly on its high temperature oxidation resistance (that is, whether the oxide film formed on the surface of the cast iron has Protective effect) and the growth of cast iron (that is, the irreversible expansion of the size of cast iron parts that work at high temperatures). These two properties are closely related to the chemical composition of cast iron. The strength and impact resistance of iron castings mainly depend on the number of alloying elements, so the study of the material of the castings becomes a very important issue. For this reason, we have conducted research on the material and made a reasonable choice of chemical composition, which not only improves the heat resistance of the casting, but also ensures the mechanical properties of the casting. The original design material of the roller is RQTSi5, and its chemical composition (%) is: wC = 2.30% ~ 2.89%, wSi = 4. 5% ~ 5.5%, wMn = 0.50% ~ 0.77%, wP = 0.06% ~ 0.09%, wS=0.062%~0.089%, wCr=0.38%~0.49%. Its mechanical properties are as follows: tensile strength 140-220MPa, hardness 160-270 HBW. The maximum operating temperature is 750~900℃. Due to the high silicon content of this material, the brittle transition temperature of cast iron is increased. Therefore, the casting is very brittle, and it is not suitable for the production of brittle-sensitive parts with uneven wall thickness. The roller plate belongs to the casting of this structure. As a result, the production has just started. At that time, a lot of waste products were caused by material problems. In addition, because the material of RQTSi5 is brittle and the yield is low, most domestic manufacturers no longer use this material to make rollers. In view of the above situation, in order to avoid batch scrapping of roll plates and ensure the smooth start of the medium and heavy plate project, trial production of an emerging material for the production of roll plates has become a top priority. Through many experiments and demonstrations, we have decided to use the new material we developed. Its chemical composition is: wC=3.05%~3.51%, wSi=2.9%~3.5%, wMn=0.24%~0.56%, wP=0.05%~ 0.09%, wS=0.010%~0.030%, wMo=0.29%~0.6%. Its mechanical properties are as follows: tensile strength 580~695MPa, elongation 8%~18%, hardness 210~280 HBW. The maximum operating temperature is 750~900℃. Due to the good properties of the materials developed and the high yield rate, it has been recognized by users.
After the material was determined, the material ingredients, spheroidization process, inoculant and inoculation process, quality control in front of the furnace, etc. were tackled and succeeded. The mechanical properties of the roller reached the best in the history of the cast iron workshop. Level.
2.Tackling key problems in smelting process
To obtain high-quality molten iron after the chemical composition is determined, a reasonable smelting process is necessary. For heat-resistant ductile iron castings, the spheroidizing treatment is particularly important (that is, the choice of inoculant and spheroidizing process). The mechanical properties of the castings are also good when the spheroidization is processed. We have selected a suitable inoculant through research and developed a reasonable spheroidization process, so that the molten iron can be well spheroidized, which not only improves the strength of the casting, but also increases its elongation, and the effect is very good.
- Selection of spheroidizing agent The quality of spheroidizing agent directly affects the spheroidizing effect, and affects the quality of molten iron and castings. Through many experiments and demonstrations, we finally determined that the spheroidizing agent adopts ReMg5-8 light rare earth, the inoculant adopts 75SiFe and the unique long-acting inoculant that can significantly improve the strength and elongation of cast iron.
- Spheroidizing To obtain high-quality castings, the selection of inoculants and spheroidizing processes is also very important. Through tackling key problems, we selected a suitable inoculant and formulated a reasonable spheroidization process, which not only increased the strength of the casting, but also increased its elongation, and the effect was very good.
The spheroidization process uses a dam bag, which must be dried thoroughly. Various alloys must be preheated. The alloys added to the dam bag from bottom to top are: light rare earth alloy 1.8% → inoculant 0.8% → cover iron plate or iron powder (according to molten iron temperature) → alkali surface 0.5%. 2/3 of the iron is tapped, and after the reaction is completed, the iron is tapped again to the required amount, and 0.6% ferromolybdenum, 0.6% inoculant are added along with the flow, and the slag is removed.
3.Tackling key problems in casting process
In order to create a high-quality project, our company has put forward requirements higher than the national standard for the surface quality, dimensional tolerances, and processing volume of the rollers. However, the rollers have large batches and tight schedules. In order to grab the schedule, the workshop had to use some casting techniques. Unfamiliar temporary workers produce roll discs, which puts forward extremely high requirements on the process of roll discs. We have made research on the casting process.
- Modeling process research It can be seen from the structure of the part that the hub is thicker and the spokes are thinner. At present, most domestic manufacturers produce castings with this structure using ordinary sand-type single-piece casting, with risers at the hub and tangential gates. With this process, the process yield rate, the rate of finished products are low, and the production efficiency is also low. If the ordinary sand mold is used for single-piece casting, the production of 5,700 rolls must be completed within the required time, 144 rolls need to be produced every day, 288 sand boxes, 16 metal molds, and sufficient molding and pouring area are required, and the craftsmanship Complex, unable to operate for workers who are unfamiliar with casting, and cannot meet production requirements. To this end, we chose the metal resin sand core stacking process through comparison, that is, the metal core box resin sand is used to make the core, and then the sand core is dropped together and put on the box ring for pouring. Only 8 sets of metal core boxes are needed to meet the production needs by adopting this process. Each sprue is poured with 3 stacks, each stack is poured with 8 pieces, and a bottom plate is poured with 48 pieces at the same time. Due to the use of the common gating system, the casting rate is high, and the surface quality of the resin sand molding castings is good.
- Design and production of tooling After the process is determined, we have designed and produced the required tooling
- The proportioning, mixing and production of core sand. The core sand preparation process is the key to the resin sand assembly core stacking process. At the beginning of production, due to the improper ratio of resin and curing agent, the sand core was difficult to remove from the metal mold, and the surface quality of the sand core was very poor. The trial production of the ratio finally determined the ratio of resin, curing agent and raw sand, and produced qualified sand cores.Proportion: 0.45~0.224mm (40/70 mesh) scrubbing sand 100%, resin is 1.8%-2% of the raw sand weight, and curing agent is 30%~-50% of the resin.Mixing: S2512C sand mixer is used for resin sand mixing. Add the weighed raw sand to the sand mixer and then add the curing agent, start mixing for 8-10 minutes, then add the resin, mix and grind for 8-10 minutes, and then output the sand .Production of sand core: wipe the inner surface of the core box clean before production, apply a release agent, pound the sand evenly when making the core, and ensure that the size is accurate when repairing the core. The prepared cores are numbered in sequence, and alcohol-based graphite is used. Brush the paint twice. After the paint is ignited, use a dry cloth to polish the surface of the sand core smoothly.
- The choice of pouring system The size of the pouring system directly affects the quality of the castings. If the area of the pouring system is too small, defects such as insufficient pouring and cold barriers are easily formed. If it is too large, it is difficult to clean it from the castings. The casting is made of ductile iron. When we first started production, we set up 4 internal runners at the head of the shaft. As a result, the roller disc was often scrapped due to the cleaning of the gate. Later, we selected a reasonable gating system through experiments based on the shape and weight of the castings, and produced qualified castings. We take full advantage of its graphitization expansion and self-feeding characteristics and adopt a non-riser feeding method of casting. Only two 80mm×40mm flat gates are opened at the head of each roller. This pouring system not only saves molten iron, but also reduces the man-hours for cleaning the pouring riser, and the surface quality of the casting is also good.
- Determination of the number of stacking rollers Using stacking pouring technology, the number of castings poured each time directly affects the quality of the castings. Too many castings are prone to shrinkage holes due to poor feeding. Too few castings, labor productivity and process yield are too low. In order to ensure the quality when the research team started the trial production, only 6 pieces per stack were poured. With the continuous accumulation of production experience, according to our careful calculation, we are now pouring 8 pieces per stack and one sprue per 3 stacks. As a result, It not only guarantees the quality of castings, but also improves labor productivity.
- Selection of pouring temperature. Castings with high pouring temperature are prone to defects such as porosity and shrinkage, while pouring temperature is too low to cause defects such as insufficient pouring and iron beans on the surface. We set a reasonable pouring temperature of 1280~1300 through experiments. ℃, produce qualified castings.
- Control of boxing time. Castings are easy to deform if boxing is too early, and it will affect later pouring. According to the size and quantity of the castings, we stipulated that the strike time is 6h.
Quality Inspection
In order to ensure the quality of the rollers produced, we have established a strict inspection system: each roller must be attached with a test block for casting testing, and the mechanical properties, metallographic structure and chemical composition of the test block are 100% tested. The unqualified ones will not leave the factory.
Production Effect
- The roller disc developed by the multi-group stacking process of metal resin sand core assembly has high strength and good surface quality. Its various properties far exceed the original design material and meet the needs of users.
- After adopting this process, the sand to iron ratio is only 1.5:1, which is far lower than the domestic advanced technology level (3~4.5):1, saving a lot of resin sand.
- The process is simple to operate and the quality is guaranteed. The cast iron workshop also produced high-quality rollers using a large number of unskilled operators.
- The productivity is increased by more than twice, which not only saves man-hours, but also saves a lot of sand box costs.
- Since multiple sets of multiple rollers use a common pouring system and no risers are required, the casting yield rate is as high as 95%, which is much higher than the 70% process yield rate of ordinary process methods. Due to the small cross-sectional area of the gating system, it can be cleaned only by lightly hammering, which greatly reduces the man-hours for cutting castings and pouring risers.
Since the roll plate produced by our company was put into production in the medium and heavy plate plant, it has been running well, working smoothly and normally, and there have been no cold bed scratches, bumps on the steel plate, or deviation of the steel plate due to the quality of the roll plate. Efficiency guarantees the normal operation of our factory’s production and creates good economic benefits.
Conclusion
Through the research on the material and casting process of the roller plate, we completed the casting task of the roller plate on time and in quality and quantity, laying the foundation for the smooth start of the medium and heavy plate project of our company. Due to the high efficiency of this process and the good surface quality of the castings, on the basis of the completion of our cooling bed rolls, we have undertaken more than 20,000 rolls production tasks from Lingang, Xianggang and other manufacturers. The promotion and application prospects are broad and economical. The benefits are very significant.
Please keep the source and address of this article for reprinting:The Casting Process Of Roulette Cast Iron Parts
Minghe Casting Company are dedicated to manufacture and provide quality and high performance Casting Parts(metal die casting parts range mainly include Thin-Wall Die Casting,Hot Chamber Die Casting,Cold Chamber Die Casting),Round Service(Die Casting Service,Cnc Machining,Mold Making,Surface Treatment).Any custom Aluminum die casting, magnesium or Zamak/zinc die casting and other castings requirements are welcome to contact us.
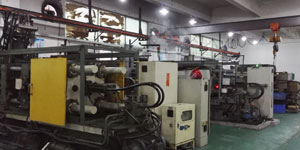
Under the control of ISO9001 and TS 16949,All processes are carried out through hundreds of advanced die casting machines, 5-axis machines, and other facilities, ranging from blasters to Ultra Sonic washing machines.Minghe not only has advanced equipment but also have professional team of experienced engineers,operators and inspectors to make the customer’s design come true.
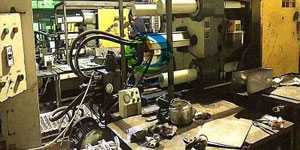
Contract manufacturer of die castings. Capabilities include cold chamber aluminum die casting parts from 0.15 lbs. to 6 lbs., quick change set up, and machining. Value-added services include polishing, vibrating, deburring, shot blasting, painting, plating, coating, assembly, and tooling. Materials worked with include alloys such as 360, 380, 383, and 413.
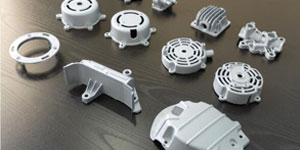
Zinc die casting design assistance/concurrent engineering services. Custom manufacturer of precision zinc die castings. Miniature castings, high pressure die castings, multi-slide mold castings, conventional mold castings, unit die and independent die castings and cavity sealed castings can be manufactured. Castings can be manufactured in lengths and widths up to 24 in. in +/-0.0005 in. tolerance.
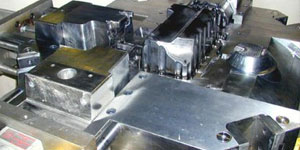
ISO 9001: 2015 certified manufacturer of die cast magnesium, Capabilities include high-pressure magnesium die casting up to 200 ton hot chamber & 3000 ton cold chamber, tooling design, polishing, molding, machining, powder & liquid painting, full QA with CMM capabilities, assembly, packaging & delivery.
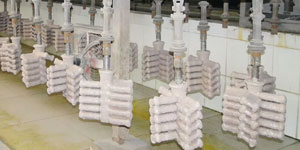
ITAF16949 certified. Additional Casting Service Include investment casting,sand casting,Gravity Casting, Lost Foam Casting,Centrifugal Casting,Vacuum Casting,Permanent Mold Casting,.Capabilities include EDI, engineering assistance, solid modeling and secondary processing.
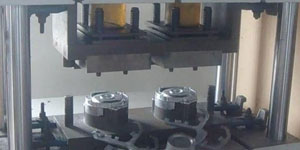
Casting Industries Parts Case Studies for: Cars, Bikes, Aircraft, Musical instruments, Watercraft, Optical devices, Sensors, Models, Electronic devices, Enclosures, Clocks, Machinery, Engines, Furniture, Jewelry, Jigs, Telecom, Lighting, Medical devices, Photographic devices, Robots, Sculptures, Sound equipment, Sporting equipment, Tooling, Toys and more.
What Can we help you do next?
∇ Go To Homepage For Die Casting China
→Casting Parts-Find out what we have done.
→Ralated Tips About Die Casting Services
By Minghe Die Casting Manufacturer |Categories: Helpful Articles |Material Tags: Aluminum Casting, Zinc Casting, Magnesium Casting, Titanium Casting, Stainless Steel Casting, Brass Casting,Bronze Casting,Casting Video,Company History,Aluminum Die Casting |Comments Off