As a measure to reduce the friction between automobile engine parts, it can be roughly divided into the following three types.
One is to reduce the actual contact area between components;
The second is to make low shear stress between parts;
The third is to reduce the input load between components.
Reducing the surface roughness of the parts helps to reduce the actual contact between the parts. On the basis of not changing the initial roughness of the surface, the surface of the mating material can be smoothed by sliding, which can further reduce the friction force.
At present, most of the engine cylinder bores are constructed by casting bushings made of gray cast iron into the aluminum alloy cylinder block. The thermal conductivity of cast iron (50W/(m·k)) is lower than that of aluminum (100W/(m·k)), and the thickness of cast iron is several mm. Recently, in order to improve the heat dissipation in the combustion chamber, cast iron sleeves are used instead of cylinder bores, and the cast iron is sprayed. This can improve the sealing of the interface and thin the tube wall, which greatly improves the heat transfer and heat transfer in this part. Heat transfer.
In addition, as a phenomenon unique to thermal spraying, a certain degree of voids are introduced into the film, and the voids are exposed on the surface layer, which can improve the oil retention of the surface of the cylinder bore.
Since it is not necessary to use the honing mesh of the conventional engine cylinder bore to ensure oil retention, the surface of the cylinder bore can be smoothed. In addition to the above-mentioned advantages of good heat transfer characteristics, it can also effectively reduce the friction from the boundary to the mixed lubrication area.
Regarding the contact between the protrusions on the surface roughness of the parts, the entire surface layer including the protrusions is used as a low shear stress material. As a method to reduce the roughness and reduce the friction alone, solid lubricants can be used.
In particular, when the surface pressure is not so high, a so-called soft coating can be used, that is, granular molybdenum disulfide (MoS2) or graphite, and tetrafluoroethylene as a solid lubricant are dispersed in polyamide resin (PAI) The coating in the medium, or the coating obtained by directly irradiating the MoS2 particles against the workpiece at a high speed. This kind of coating can be applied to the surface layer of piston rod and crankshaft bearing alloy with large contact area in engine parts.
On the other hand, for parts with high surface pressure, we have developed a DLC coating that has the same low friction coefficient as a solid lubricant when it is hard and non-lubricated, so that the same effect can be obtained under lubrication. Coating.
This article will introduce the DLC film that does not contain hydrogen (hydrogen-free DLC film) and the DLC film that contains Si (Si-DLC). The two are very different from the past in terms of surface treatment and design thinking in that the coating itself has no separate characteristics, and the combination of the lubricating oil or the moisture in the lubricating oil can significantly reduce the friction.
In order to reduce the friction between the piston ring and the cylinder bore, in recent years, CrN film has been used to replace the previous Cr plating or nitriding technology. The thickness of the Cr-plated film is about 100, while the thickness of the CrN film with good wear resistance is only 25, which can reduce the deviation range of the film thickness. As a result, without changing the lower limit of the piston ring tension, and only setting the intermediate value to be smaller, the friction between the piston ring and the cylinder bore can be reduced.
In addition, since the amount of wear of the CrN film is small, the initial curvature of the outer surface of the piston ring can be maintained, and the increased contact range due to wear can be suppressed, which also helps to reduce friction.
Please keep the source and address of this article for reprinting: Technology to reduce friction of automobile engine parts
Minghe Die Casting Company are dedicated to manufacture and provide quality and high performance Casting Parts(metal die casting parts range mainly include Thin-Wall Die Casting,Hot Chamber Die Casting,Cold Chamber Die Casting),Round Service(Die Casting Service,Cnc Machining,Mold Making,Surface Treatment).Any custom Aluminum die casting, magnesium or Zamak/zinc die casting and other castings requirements are welcome to contact us.
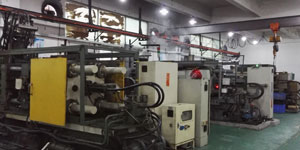
Under the control of ISO9001 and TS 16949,All processes are carried out through hundreds of advanced die casting machines, 5-axis machines, and other facilities, ranging from blasters to Ultra Sonic washing machines.Minghe not only has advanced equipment but also have professional team of experienced engineers,operators and inspectors to make the customer’s design come true.
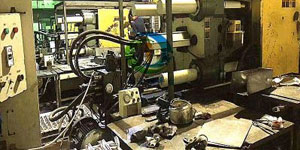
Contract manufacturer of die castings. Capabilities include cold chamber aluminum die casting parts from 0.15 lbs. to 6 lbs., quick change set up, and machining. Value-added services include polishing, vibrating, deburring, shot blasting, painting, plating, coating, assembly, and tooling. Materials worked with include alloys such as 360, 380, 383, and 413.
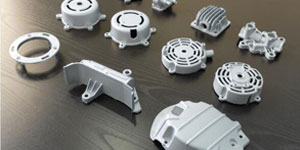
Zinc die casting design assistance/concurrent engineering services. Custom manufacturer of precision zinc die castings. Miniature castings, high pressure die castings, multi-slide mold castings, conventional mold castings, unit die and independent die castings and cavity sealed castings can be manufactured. Castings can be manufactured in lengths and widths up to 24 in. in +/-0.0005 in. tolerance.
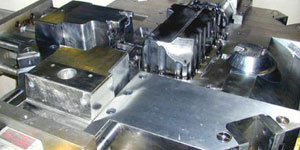
ISO 9001: 2015 certified manufacturer of die cast magnesium, Capabilities include high-pressure magnesium die casting up to 200 ton hot chamber & 3000 ton cold chamber, tooling design, polishing, molding, machining, powder & liquid painting, full QA with CMM capabilities, assembly, packaging & delivery.
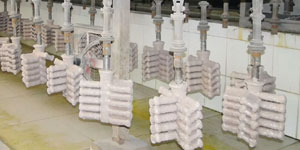
ITAF16949 certified. Additional Casting Service Include investment casting,sand casting,Gravity Casting, Lost Foam Casting,Centrifugal Casting,Vacuum Casting,Permanent Mold Casting,.Capabilities include EDI, engineering assistance, solid modeling and secondary processing.
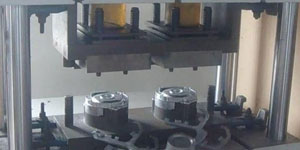
Casting Industries Parts Case Studies for: Cars, Bikes, Aircraft, Musical instruments, Watercraft, Optical devices, Sensors, Models, Electronic devices, Enclosures, Clocks, Machinery, Engines, Furniture, Jewelry, Jigs, Telecom, Lighting, Medical devices, Photographic devices, Robots, Sculptures, Sound equipment, Sporting equipment, Tooling, Toys and more.
What Can we help you do next?
∇ Go To Homepage For Die Casting China
→Casting Parts-Find out what we have done.
→Ralated Tips About Die Casting Services
By Minghe Die Casting Manufacturer |Categories: Helpful Articles |Material Tags: Aluminum Casting, Zinc Casting, Magnesium Casting, Titanium Casting, Stainless Steel Casting, Brass Casting,Bronze Casting,Casting Video,Company History,Aluminum Die Casting |Comments Off