The normal blast furnace operation type is characterized by smooth inner wall surface and stable slag skin. However, in actual blast furnace production, due to the influence of changes in the slagging system, charging system, air supply system, thermal system, and external raw materials, the blast furnace operating furnace model will undergo changes such as sticking or slag peeling, which will affect the blast furnace. This will cause serious slag peeling, which will also cause large-area damage to the cooling stave.
The main factors of furnace wall adhesion are:
1. The raw material contains high powder content, the edge gas flow does not develop, and the edge pipeline occurs;
2. The slagging system is unstable, the slag performance changes greatly, and the slag-iron fluidity is poor, which is easy to cause the furnace wall to stick;
3. Poor furnace temperature control, large fluctuations, and frequent fluctuations of the blast furnace soft melting zone;
4. Long-term smelting of high-silicon and low-sulfur iron is high, and the slag fluidity is poor;
5. Cooling wall leakage or changes in cooling water pressure and water temperature cause excessive cooling intensity;
6. The cloth system is unreasonable, resulting in local edge airflow or edge ducts.
The main factors that cause the slag skin of the furnace wall to fall off in a large area are: the air supply system and the charging system are unreasonable, and the edge airflow develops; the change of the cooling system causes the cooling intensity to be low, and the stable slag skin cannot be formed.
When the furnace conditions change, measures must be taken in time. The general control methods adopted are:
1. The distribution characteristics determine the gas flow distribution, which in turn determines the distribution of the temperature field in the furnace and the shape and position of the reflow zone. Especially the reflow behavior of the charge at the furnace wall will cause the slag skin to thicken or fall off. The adjustment of the distribution system and effective control of the distribution of gas flow are important means to restore the blast furnace type to normal.
When the furnace wall is stuck, the main measures should be taken to lay the edge, and the edge airflow should be properly developed. When the slag skin falls off the furnace wall, edge pressure measures should be taken to control the edge gas flow.
2. Control the furnace temperature and slag basicity, treat furnace wall adhesion, appropriately control the furnace temperature at the upper limit level, strictly forbid low furnace temperature operation, lower the slag basicity, and the sulfur content of pig iron is mainly second-class iron to ensure good The fluidity of slag iron.
3. Control the cooling intensity. When the slag skin is not easy to form when the slag skin falls off, the water pressure should be increased to increase the cooling intensity of the part. When bonding occurs, the water pressure should be appropriately reduced to reduce the cooling strength of the part.
4. When dealing with the adhesion of the lower part, properly wash the furnace
Please keep the source and address of this article for reprinting:Summary of changing factors and control methods of blast furnace type
Minghe Die Casting Company are dedicated to manufacture and provide quality and high performance Casting Parts(metal die casting parts range mainly include Thin-Wall Die Casting,Hot Chamber Die Casting,Cold Chamber Die Casting),Round Service(Die Casting Service,Cnc Machining,Mold Making,Surface Treatment).Any custom Aluminum die casting, magnesium or Zamak/zinc die casting and other castings requirements are welcome to contact us.
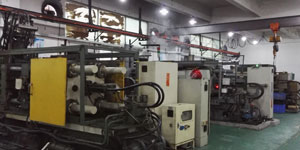
Under the control of ISO9001 and TS 16949,All processes are carried out through hundreds of advanced die casting machines, 5-axis machines, and other facilities, ranging from blasters to Ultra Sonic washing machines.Minghe not only has advanced equipment but also have professional team of experienced engineers,operators and inspectors to make the customer’s design come true.
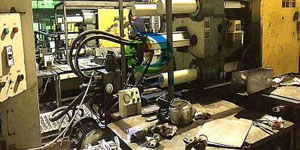
Contract manufacturer of die castings. Capabilities include cold chamber aluminum die casting parts from 0.15 lbs. to 6 lbs., quick change set up, and machining. Value-added services include polishing, vibrating, deburring, shot blasting, painting, plating, coating, assembly, and tooling. Materials worked with include alloys such as 360, 380, 383, and 413.
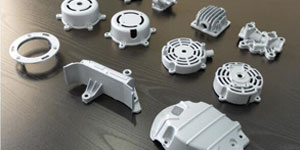
Zinc die casting design assistance/concurrent engineering services. Custom manufacturer of precision zinc die castings. Miniature castings, high pressure die castings, multi-slide mold castings, conventional mold castings, unit die and independent die castings and cavity sealed castings can be manufactured. Castings can be manufactured in lengths and widths up to 24 in. in +/-0.0005 in. tolerance.
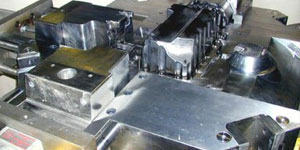
ISO 9001: 2015 certified manufacturer of die cast magnesium, Capabilities include high-pressure magnesium die casting up to 200 ton hot chamber & 3000 ton cold chamber, tooling design, polishing, molding, machining, powder & liquid painting, full QA with CMM capabilities, assembly, packaging & delivery.
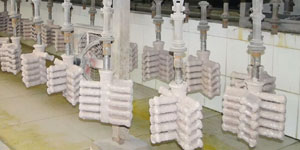
ITAF16949 certified. Additional Casting Service Include investment casting,sand casting,Gravity Casting, Lost Foam Casting,Centrifugal Casting,Vacuum Casting,Permanent Mold Casting,.Capabilities include EDI, engineering assistance, solid modeling and secondary processing.
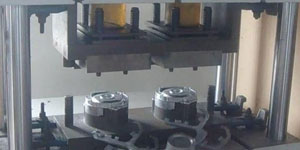
Casting Industries Parts Case Studies for: Cars, Bikes, Aircraft, Musical instruments, Watercraft, Optical devices, Sensors, Models, Electronic devices, Enclosures, Clocks, Machinery, Engines, Furniture, Jewelry, Jigs, Telecom, Lighting, Medical devices, Photographic devices, Robots, Sculptures, Sound equipment, Sporting equipment, Tooling, Toys and more.
What Can we help you do next?
∇ Go To Homepage For Die Casting China
→Casting Parts-Find out what we have done.
→Ralated Tips About Die Casting Services
By Minghe Die Casting Manufacturer |Categories: Helpful Articles |Material Tags: Aluminum Casting, Zinc Casting, Magnesium Casting, Titanium Casting, Stainless Steel Casting, Brass Casting,Bronze Casting,Casting Video,Company History,Aluminum Die Casting |Comments Off