1 What are the factors that affect the “aging” of water glass? How to eliminate the “aging” of water glass?
The freshly prepared water glass is a true solution. However, during the storage process, the silicic acid in the water glass will undergo condensation polymerization, which will gradually polycondensate from the true solution into a macromolecular silicic acid solution, and finally become a silicic acid gel. Therefore, water glass is actually a heterogeneous mixture composed of polysilicic acid with different degrees of polymerization, which is easily affected by its modulus, concentration, temperature, electrolyte content and storage time.
During storage, the molecules of water glass undergo condensation polymerization to form a gel, and its bonding strength gradually decreases with the extension of storage time. This phenomenon is called “aging” of water glass.
The “aging” phenomenon can be explained by the following two sets of test data: high modulus water glass (M=2.89, ρ=1.44g/cm3) after 20, 60, 120, 180, 240 days of storage, the CO2 hardened water glass is blown The dry tensile strength of sand drops correspondingly by 9.9%, 14%, 23.5%, 36.8% and 40%; low modulus sodium silicate (M=2.44, ρ=1.41g/cm3) is stored for 7, 30, 60 and 90 days after being dried. The tensile strength decreased by 4.5%, 5%, 7.3% and 11% respectively.
The storage time of water glass has little effect on the initial strength of ester-hardened water glass self-hardening sand, but it has a significant effect on the later strength. According to measurements, it is reduced by about 60% for high modulus water glass, and 15-20% for low modulus water glass. . The residual strength also decreases with the extension of storage time.
During the storage of water glass, the polycondensation and depolymerization of polysilicic acid proceed at the same time, the molecular weight is disproportionated, and finally a multi-dispersed system in which monoorthosilicic acid and colloidal particles coexist is formed. That is, during the aging process of water glass, The degree of polymerization of silicic acid is disproportionated, and the content of monoorthosilicic acid and high polysilicic acid increases with the extension of storage time. As a result of condensation polymerization and depolymerization reaction of water glass during storage, the bonding strength is reduced, that is, the phenomenon of “aging” occurs.
The main factors affecting the “aging” of water glass are: storage time, modulus and concentration of water glass. The longer the storage time, the higher the modulus and the greater the concentration, the more serious the “aging”.
The long-existing water glass can be modified in a variety of ways to eliminate “aging” and restore the water glass to the performance of fresh water glass:
1. Physical modification
The aging of water glass is a spontaneous process that slowly releases energy. The physical modification of “aged” water glass is to use magnetic field, ultrasound, high frequency or heating to provide energy to the water glass system and promote the high polymerization of polysilicate glue. The particles re-depolymerize and promote the homogenization of the molecular weight of polysilicic acid, thereby eliminating the aging phenomenon, which is the mechanism of physical modification. For example, after treatment with a magnetic field, the strength of sodium silicate sand is increased by 20-30%, the amount of sodium silicate added is reduced by 30-40%, CO2 is saved, collapsibility is improved, and there are good economic benefits.
The disadvantage of physical modification is that it is not durable, and the bonding strength will decrease when stored after treatment, so it is suitable for use as soon as possible after treatment in the foundry. Especially for water glass with M>2.6, the concentration of silicic acid molecules is large, and after physical modification and depolymerization, it will polycondensate relatively quickly. It is best to use it immediately after treatment.
2. Chemical modification
Chemical modification is to add a small amount of compounds to the water glass, these compounds all contain carboxyl, amide, carbonyl, hydroxyl, ether, amino and other polar groups, which are adsorbed on silicic acid molecules or colloidal particles through hydrogen bonds or static electricity. Surface, change its surface potential energy and solvation ability, improve the stability of polysilicic acid, thereby preventing “aging” from proceeding.
For example, adding polyacrylamide, modified starch, polyphosphate, etc. to the water glass can achieve better results.
Incorporating organic matter into ordinary water glass or even modified water glass can play a variety of functions, such as: changing the viscous flow properties of water glass; improving the modeling performance of water glass mixtures; increasing the bonding strength to make the water glass absolutely added The amount is reduced; the plasticity of the silicic acid gel is improved; the residual strength is reduced, so that the water glass sand is more suitable for cast iron and non-ferrous alloys.
3. Physical-chemical modification
Physical modification is suitable for “aged” water glass, and it can be used immediately after modification. Chemical modification is suitable for processing fresh water glass, and the modified water glass can be stored for a long time. The combination of physical modification and chemical modification can make the water glass have a lasting modification effect. For example, adding polyacrylamide to the autoclave to modify the “aging” water glass has a good effect. Among them, the pressure and the pressure of the autoclave are used. Stirring is a physical modification, and adding polyacrylamide is a chemical modification.
2 How to prevent CO2 blowing hardened sodium silicate sand mold (core) surface chalking?
After soda sodium silicate sand is blown CO2 hardened and left for a period of time, sometimes a substance like hoar frost will appear on the surface of the lower mold (core), which will seriously reduce the surface strength of the place and easily produce sand washing defects during pouring. According to analysis, the main component of this white substance is NaHCO3, which may be caused by excessive moisture or CO2 in the sodium silicate sand. The reaction is as follows:
Na2CO3+H2O→NaHCO3+NaOH
Na2O+2CO2+H2O→2NaHCO3
NaHCO3 easily migrates outwards with moisture, causing powdery like frost on the surface of the mold and core.
The solution is as follows:
1. Control the moisture content of the sodium silicate sand not to be too high (especially in the rainy season and winter).
2. The time for blowing CO2 should not be too long.
3. The hardened mold and core should not be placed for a long time, and should be molded and poured in time.
4. Adding about 1% (mass fraction) of the syrup with a density of 1.3g/cm3 to the sodium silicate sand can effectively prevent the surface from powdering.
3 How to improve the moisture absorption resistance of the water glass sand mold (core)?
The soda water glass sand core hardened by CO2 or heating methods is assembled in the wet clay mold. If it is not poured in time, the strength of the sand core will decrease sharply, not only may creep, even collapse; it is stored in a humid environment The strength of the sand core is also significantly reduced. Table 1 shows the strength value of the CO2 hardened sodium water glass sand core when placed in an environment with a relative humidity of 97% for 24 hours. The reason for the loss of strength when stored in a humid environment is due to the re-hydration of sodium water glass. The Na+ and OH— in the sodium silicate binder matrix absorb moisture and erodes the matrix, finally breaking the silicon-oxygen bond Si—O—Si, resulting in a significant decrease in the bonding strength of the sodium silicate sand.
1. Lithium water glass is added to sodium water glass, or Li2CO3, CaCO3, ZnCO3 and other inorganic additives are added to sodium water glass, because relatively insoluble carbonates and silicates can be formed, and free sodium ions can be reduced Therefore, the moisture absorption resistance of the sodium water glass binder can be improved.
2. Add a small amount of organic material or organic matter with surfactant function to the sodium water glass. When the binder is hardened, the hydrophilic Na+ and OH- ions in the sodium water glass gel may be substituted by organic hydrophobic groups, or Combined with each other, the exposed organic hydrophobic base improves moisture absorption.
3. Improve the modulus of water glass, because the moisture resistance of high modulus water glass is stronger than that of low modulus water glass.
4. Add starch hydrolysate to sodium silicate sand. A better method is to use starch hydrolyzate to modify sodium water glass.
4 What are the characteristics of the CO2 blowing hardened water glass-alkaline phenolic resin sand composite process?
In recent years, in order to improve the quality of steel castings, some small and medium-sized enterprises urgently need to adopt the resin sand process. However, due to limited economic capacity, they are unable to purchase resin sand regeneration equipment, and the old sand cannot be recycled, resulting in high production costs. In order to find an effective way to improve the quality of castings without increasing the cost too much, the process characteristics of CO2 blowing hardened sodium silicate sand and CO2 blowing hardened alkaline phenolic resin sand can be combined, and CO2 blowing hardened sodium silicate—alkaline phenolic resin can be used. The resin sand compounding process uses alkaline phenolic resin sand as the surface sand and water glass sand as the back sand, while blowing CO2 for hardening.
The phenolic resin used in CO2-alkaline phenolic resin sand is made by polycondensation of phenol and formaldehyde under the action of a strong alkaline catalyst and adding a coupling agent. Its PH value is ≥13, and its viscosity is ≤500mPa•s. The amount of phenolic resin added to the sand is 3% to 4% (mass fraction). When the CO2 flow rate is 0.8~1.0m3/h, the best blowing time is 30~60s; if the blowing time is too short, the hardening strength of the sand core will be low; if the blowing time is too long, the strength of the sand core will not increase, and it is wasted gas.
CO2—Alkaline phenolic resin sand does not contain harmful elements such as N, P, S, etc., so casting defects such as pores, surface microcracks, etc. caused by these elements are eliminated; harmful gases such as H2S and SO2 are not released during pouring, which is beneficial to environmental protection ; Good collapsibility, easy to clean; high dimensional accuracy; high production efficiency.
The CO2 blowing hardened water glass-alkaline phenolic resin sand composite process can be widely used in steel castings, iron castings, copper alloys and light alloy castings.
The composite process is a simple and convenient process. The process is as follows: firstly mix resin sand and sodium silicate sand separately, and then put them into two sand buckets; then add the mixed resin sand as surface sand into the sand box And pound, the thickness of the surface sand layer is generally 30-50mm; then water glass sand is added to make the back sand to fill and compact; finally, CO2 gas is blown into the mold for hardening.
The diameter of the blowing tube is generally 25mm, and the hardenable range is about 6 times the diameter of the blowing tube.
The blowing time depends on the size, shape, gas flow, and area of the exhaust plug of the sand mold (core). Generally, the blowing time is controlled within 15~40s.
After blowing the hard sand mold (core), the mold can be taken. The strength of the sand mold (core) rises quickly. Brush the paint within half an hour after taking the mold, and close the box for pouring after 4 hours.
The composite process is particularly suitable for steel casting plants that do not have resin sand regeneration equipment and need to produce high-quality castings. The process is simple and easy to control, and the quality of the produced castings is equivalent to that of other resin sand castings.
CO2 blowing hardened sodium silicate sand can also be compounded with CO2 blowing hardened sodium polyacrylate resin sand for the production of various high-quality castings.
5 What are the pros and cons of the CO2-organic ester composite hardened sodium silicate sand process?
In recent years, the CO2-organic ester composite hardened sodium silicate sand process has a trend of expanding applications. The process is as follows: add a certain amount of organic ester during sand mixing (usually half of the normal required amount or 4~6% of the weight of water glass); after the modeling is completed, blow CO2 to harden to the mold release strength (compressive resistance is generally required) The strength is about 0.5MPa); after demolding, the organic ester continues to harden, and the strength of the molding sand rises at a faster rate; after the CO2 is blown and placed for 3~6h, the sand mold can be combined and poured.
The hardening mechanism is:
When the water glass sand blows CO2, under the action of the gas pressure difference and the concentration difference, the CO2 gas will try to flow in all directions of the molding sand. After the CO2 gas contacts the water glass, it immediately reacts with it to form a gel. Due to the diffusion effect, the reaction is always from the outside to the inside, and the outer layer first forms a gel film, which prevents the CO2 gas and the water glass from continuing to react. Therefore, in a short time, no matter what method is used to control CO2 gas, it is impossible to make it react with all water glass. According to analysis, when the molding sand reaches the best blowing strength, the water glass reacted with CO2 gas is about 65%. This means that the water glass does not fully exert its bonding effect, and at least 35% of the water glass does not react. The organic ester hardener can form a uniform mixture with the binder, and can give full play to the bonding effect of the binder. All parts of the core sand build up strength at the same speed.
Increasing the amount of water glass added will increase the final strength of the sand mold, but its residual strength will also increase, making it difficult to clean the sand. When the added amount of water glass is too small, the final strength is too small and cannot meet the requirements for use. In actual production, the amount of water glass added is generally controlled at about 4%.
When using organic ester alone to harden, the general amount of organic ester added is 8-15% of the amount of water glass. When using composite hardening, it is estimated that about half of the water glass has been hardened when CO2 is blown, and about half of the water glass has not hardened yet. Therefore, it is more appropriate for the amount of organic esters to account for 4 to 6% of the amount of water glass.
The composite hardening method can give full play to the dual advantages of CO2 hardening and organic ester hardening, and can fully exert the bonding effect of water glass to achieve fast hardening speed, early mold release, high strength, good collapsibility, and low cost. Comprehensive effect.
However, the CO2-organic ester composite hardening process needs to add 0.5 to 1% more water glass than the simple organic ester hardening method, which will increase the difficulty of the regeneration of the used water glass sand.
6 Why is it easy to produce sticky sand when the sodium silicate sand process is used to produce iron castings? How to prevent it?
When the sand mold (core) made of sodium silicate sand is used for pouring iron castings, serious sticky sand is often produced, which limits its application in the production of cast iron.
The Na2O, SiO2 in the sodium silicate sand and the iron oxide produced by the liquid metal during pouring form low-melting silicate. As mentioned earlier, if this compound contains more fusible amorphous glass, the bonding force between this layer of glass and the surface of the casting is very small, and the shrinkage coefficient is different from that of the metal. Large stress is easy to remove from the surface of the casting without sand sticking. If the compound formed on the surface of the casting has a high content of SiO2 and a low content of FeO, MnO, etc., its solidified structure basically has a crystalline structure, which will be firmly combined with the casting, resulting in sticky sand.
When the sodium silicate sand is used to produce iron castings, due to the low pouring temperature and high carbon content of the iron castings, iron and manganese are not easily oxidized, and the resulting sticky sand layer has a crystalline structure, and it is difficult to establish a suitable layer between the iron castings and the sticky sand layer. The thickness of the iron oxide layer is different from the resin sand between the casting and the sticky sand layer, which can produce a bright carbon film through resin pyrolysis when producing iron castings, so the sticky sand layer is not easy to remove.
In order to prevent the production of soda water glass sand from the production of iron castings, suitable coatings can be used. Such as water-based paint, the surface needs to be dried after painting, so alcohol-based quick-drying paint is best.
In general, iron castings can also add an appropriate amount of coal powder (such as 3% to 6%) (mass fraction) to the sodium silicate sand, so that the pyrolysis of the coal powder between the casting and the sand layer can produce a bright carbon film. It is not wetted by metals and their oxides, so that the sticky sand layer is easily peeled off from the casting.
7 Is sodium silicate sand expected to become environmentally friendly moulding sand with no waste sand discharge?
Water glass is colorless, odorless, and non-toxic. It will not cause serious problems if it touches the skin and clothes and rinses with water, but it must be avoided to splash into the eyes. Water glass has no irritating or harmful gases released during sand mixing, modeling, hardening and pouring, and there is no black and acid pollution. However, if the process is improper and too much sodium silicate is added, the collapsibility of the sodium silicate sand will not be good, and the dust will fly during sand cleaning, which will also cause pollution. At the same time, it is difficult to regenerate old sand, and the discharge of waste sand causes alkaline pollution to the environment.
If these two problems can be overcome, sodium silicate sand can become environmentally friendly molding sand with basically no waste sand discharge.
The fundamental measure to solve these two problems is to reduce the amount of water glass added to less than 2%, which can basically shake off the sand. When the amount of water glass added is reduced, the residual Na2O in the old sand is also reduced. Using a relatively simple dry regeneration method, it is possible to maintain the residual Na2O in the circulating sand below 0.25%. This reclaimed sand can meet the application requirements of single molding sand for small and medium-sized steel castings. At this time, even if the old sodium silicate sand does not use the expensive and complicated wet method to regenerate, but the relatively simple and cheap dry method is used, it can be fully recycled, basically no waste sand is discharged, and the ratio of sand to iron It can be reduced to less than 1:1.
8 How to effectively regenerate sodium silicate sand?
If the residual Na2O in the old sodium silicate sand is too high, after adding the sodium silicate to the sand, the molding sand will not have enough usable time, and the accumulation of too much Na2O will deteriorate the refractoriness of the quartz sand. Therefore, the residual Na2O should be removed as much as possible when regenerating the used sodium silicate sand.
Please keep the source and address of this article for reprinting:Several problems that should be paid attention to in sodium silicate sand casting
Minghe Die Casting Company are dedicated to manufacture and provide quality and high performance Casting Parts(metal die casting parts range mainly include Thin-Wall Die Casting,Hot Chamber Die Casting,Cold Chamber Die Casting),Round Service(Die Casting Service,Cnc Machining,Mold Making,Surface Treatment).Any custom Aluminum die casting, magnesium or Zamak/zinc die casting and other castings requirements are welcome to contact us.
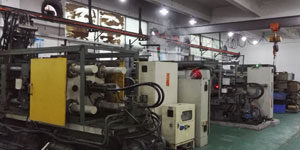
Under the control of ISO9001 and TS 16949,All processes are carried out through hundreds of advanced die casting machines, 5-axis machines, and other facilities, ranging from blasters to Ultra Sonic washing machines.Minghe not only has advanced equipment but also have professional team of experienced engineers,operators and inspectors to make the customer’s design come true.
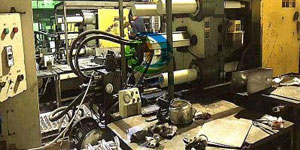
Contract manufacturer of die castings. Capabilities include cold chamber aluminum die casting parts from 0.15 lbs. to 6 lbs., quick change set up, and machining. Value-added services include polishing, vibrating, deburring, shot blasting, painting, plating, coating, assembly, and tooling. Materials worked with include alloys such as 360, 380, 383, and 413.
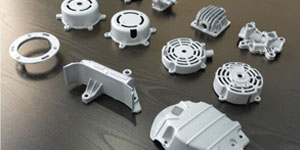
Zinc die casting design assistance/concurrent engineering services. Custom manufacturer of precision zinc die castings. Miniature castings, high pressure die castings, multi-slide mold castings, conventional mold castings, unit die and independent die castings and cavity sealed castings can be manufactured. Castings can be manufactured in lengths and widths up to 24 in. in +/-0.0005 in. tolerance.
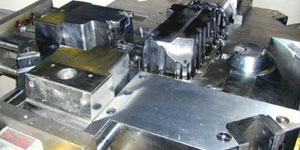
ISO 9001: 2015 certified manufacturer of die cast magnesium, Capabilities include high-pressure magnesium die casting up to 200 ton hot chamber & 3000 ton cold chamber, tooling design, polishing, molding, machining, powder & liquid painting, full QA with CMM capabilities, assembly, packaging & delivery.
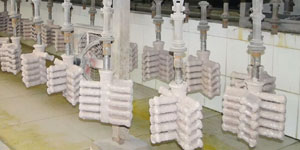
ITAF16949 certified. Additional Casting Service Include investment casting,sand casting,Gravity Casting, Lost Foam Casting,Centrifugal Casting,Vacuum Casting,Permanent Mold Casting,.Capabilities include EDI, engineering assistance, solid modeling and secondary processing.
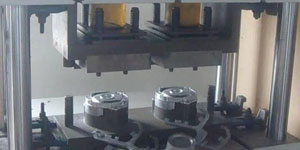
Casting Industries Parts Case Studies for: Cars, Bikes, Aircraft, Musical instruments, Watercraft, Optical devices, Sensors, Models, Electronic devices, Enclosures, Clocks, Machinery, Engines, Furniture, Jewelry, Jigs, Telecom, Lighting, Medical devices, Photographic devices, Robots, Sculptures, Sound equipment, Sporting equipment, Tooling, Toys and more.
What Can we help you do next?
∇ Go To Homepage For Die Casting China
→Casting Parts-Find out what we have done.
→Ralated Tips About Die Casting Services
By Minghe Die Casting Manufacturer |Categories: Helpful Articles |Material Tags: Aluminum Casting, Zinc Casting, Magnesium Casting, Titanium Casting, Stainless Steel Casting, Brass Casting,Bronze Casting,Casting Video,Company History,Aluminum Die Casting |Comments Off