The generation of subcutaneous pores is a comprehensive reaction of improper operation of various links and procedures in the casting process. The reasons for formation are complex, and there are many influencing factors. Everyone is involved, and every process should arouse everyone’s attention.
1. Raw materials
1. The use of raw materials with high titanium (Ti) and aluminum (AI) content, high-alloy steel, stainless steel, etc. is prohibited.
2. Raw materials with serious corrosion and oxidation, oil, coal slime, and waste sand should be cleaned up and used.
3. Use wet and watery raw materials after drying. 4. Thin iron sheets (pipe fittings) less than 3mm are forbidden to use. 5. The length of raw materials should be controlled at about 300-400mm.
2. Hot metal smelting
1. When the raw materials are loaded into the furnace, they must be compact and minimize the space to reduce the hot metal inhalation and oxidation.
2. In each furnace of molten iron melting process, thoroughly remove the slag at least 2-3 times, and after removing the slag, cover the molten iron with slag accumulation and insulation materials in time to avoid long-term contact of the molten iron with air to inhale and oxidize.
3. For the molten iron, the waiting time at high temperature should not exceed 10-15 minutes, otherwise the quality of the molten iron will be seriously deteriorated and become “dead water”.
4. The tapping temperature should not be lower than 1540±10℃. After tapping, the slag should be removed in time, and at the same time covered with slag heat-preserving agent to prevent the molten iron from cooling and oxidizing.
5. Recarburizers that do not meet the standards are prohibited.
3. Inoculants
1. It should be baked at 300-400℃ before use to remove the adsorbed moisture and crystal water. 2. The particle size of the inoculant is 5-10mm. 3. The aluminum content of the inoculant is less than 1%. 4. Pouring
1. Large and small bags must be dried thoroughly. Wet bags are forbidden to use. It is strictly forbidden to replace drying with hot metal bags.
2. Increase pouring temperature, quick pouring at high temperature. Pouring principle: slow-fast-slow. Practice has proved that increasing the pouring temperature by 30-50°C can greatly reduce the occurrence of porosity. When pouring, the molten iron should always be filled with the sprue, with continuous flow in the middle, so as to quickly establish the static pressure of the molten iron and resist the intrusion of interface gas.
3. Small ladle hot metal is forbidden if the temperature is lower than 1350℃, it should be used after returning to the furnace to raise the temperature. 4. Strengthen the slag blocking and slag shielding, and remove the oxide scale in time to prevent it from being brought into the cavity. .
Four, sand mixing
1. Strictly control the moisture of the molding sand not more than 3.5%.
2. The air permeability of the molding sand is controlled at 130-180, the wet compressive strength is 120-140KPa, the compaction rate is 35-38%, and the surface hardness of the molding sand is >90. 3. Use high-quality bentonite and coal powder.
4. Add new sand as required.
5. At the end of the sand mixing every day, the excess sand should be recovered, and the sand mixer should be thoroughly cleaned and cleaned.
Five, mold and modeling
1. The parting surface of the mold should be equipped with vent grooves or vents and dark air chambers to reduce gas pressure.
2. Add a dark gas chamber to the mold to reduce gas pressure.
3. Sprinkle cryolite powder on the runner or sand core (the amount will be determined after passing the test).
Six, core making
1. The water content of silica sand is less than 0.2%, and the mud content is less than 0.3%.
2. Core making process: Before sand mixing, silica sand needs to be heated to 25-35°C, first add component 1 to the sand and mix for 1-2 minutes, then add component 2, and continue mixing for 1-2 minutes. The addition amount of the two components is 0.75% of the mass fraction of sand.
3. Due to the high sensitivity of polyisocyanate to water, the storage time of the prepared sand core should not exceed 24 hours.
4. Too high concentration and residual amount of triethylamine may cause subcutaneous pores in castings.
Please keep the source and address of this article for reprinting: Measures and Suggestions to Solve the Subcutaneous Porosity of Castings
Minghe Die Casting Company are dedicated to manufacture and provide quality and high performance Casting Parts(metal die casting parts range mainly include Thin-Wall Die Casting,Hot Chamber Die Casting,Cold Chamber Die Casting),Round Service(Die Casting Service,Cnc Machining,Mold Making,Surface Treatment).Any custom Aluminum die casting, magnesium or Zamak/zinc die casting and other castings requirements are welcome to contact us.
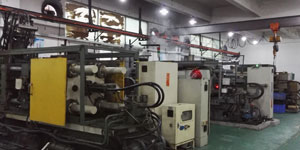
Under the control of ISO9001 and TS 16949,All processes are carried out through hundreds of advanced die casting machines, 5-axis machines, and other facilities, ranging from blasters to Ultra Sonic washing machines.Minghe not only has advanced equipment but also have professional team of experienced engineers,operators and inspectors to make the customer’s design come true.
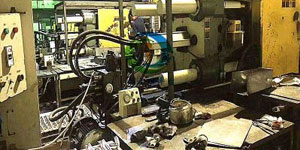
Contract manufacturer of die castings. Capabilities include cold chamber aluminum die casting parts from 0.15 lbs. to 6 lbs., quick change set up, and machining. Value-added services include polishing, vibrating, deburring, shot blasting, painting, plating, coating, assembly, and tooling. Materials worked with include alloys such as 360, 380, 383, and 413.
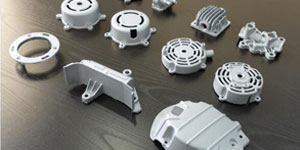
Zinc die casting design assistance/concurrent engineering services. Custom manufacturer of precision zinc die castings. Miniature castings, high pressure die castings, multi-slide mold castings, conventional mold castings, unit die and independent die castings and cavity sealed castings can be manufactured. Castings can be manufactured in lengths and widths up to 24 in. in +/-0.0005 in. tolerance.
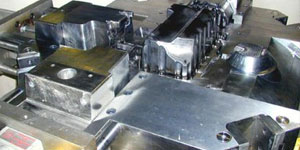
ISO 9001: 2015 certified manufacturer of die cast magnesium, Capabilities include high-pressure magnesium die casting up to 200 ton hot chamber & 3000 ton cold chamber, tooling design, polishing, molding, machining, powder & liquid painting, full QA with CMM capabilities, assembly, packaging & delivery.
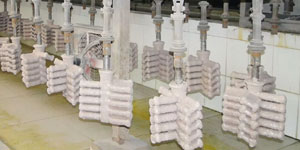
ITAF16949 certified. Additional Casting Service Include investment casting,sand casting,Gravity Casting, Lost Foam Casting,Centrifugal Casting,Vacuum Casting,Permanent Mold Casting,.Capabilities include EDI, engineering assistance, solid modeling and secondary processing.
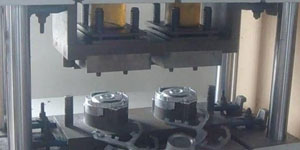
Casting Industries Parts Case Studies for: Cars, Bikes, Aircraft, Musical instruments, Watercraft, Optical devices, Sensors, Models, Electronic devices, Enclosures, Clocks, Machinery, Engines, Furniture, Jewelry, Jigs, Telecom, Lighting, Medical devices, Photographic devices, Robots, Sculptures, Sound equipment, Sporting equipment, Tooling, Toys and more.
What Can we help you do next?
∇ Go To Homepage For Die Casting China
→Casting Parts-Find out what we have done.
→Ralated Tips About Die Casting Services
By Minghe Die Casting Manufacturer |Categories: Helpful Articles |Material Tags: Aluminum Casting, Zinc Casting, Magnesium Casting, Titanium Casting, Stainless Steel Casting, Brass Casting,Bronze Casting,Casting Video,Company History,Aluminum Die Casting |Comments Off