1. Graphitization process of cast iron
The formation process of graphite in cast iron is called graphitization process. The basic process of the structure of cast iron is the formation process of graphite in cast iron. Therefore, it is very important to understand the conditions and influencing factors of the graphitization process to master the structure and properties of cast iron materials.
According to the dual state diagram of Fe-C alloy, the graphitization process of cast iron can be divided into three stages:
The first stage is the liquid phase hypoeutectic crystallization stage. Including the direct crystallization of primary graphite from the liquid phase of hypereutectic components and the liquid phase of eutectic components to crystallize austenite plus graphite, graphite formed by decomposing primary cementite and eutectic cementite during high temperature annealing.
The intermediate stage is the stage between eutectic transformation and hypoeutectoid transformation. Including the direct precipitation of secondary graphite from austenite and the graphite formed by the decomposition of secondary cementite in this temperature range.
The third stage, that is, the transformation phase of the total discount. Including the eutectoid graphite formed during the co-folding transformation and the graphite formed by the decomposition of the eutectoid cementite during annealing.
2. Factors affecting graphitization of cast iron
The structure of cast iron depends on the degree of graphitization. In order to obtain the required structure, the key is to control the degree of graphitization. Practice has proved that many factors such as the chemical composition of cast iron, the cooling rate of cast iron crystals, the overheating and standing of molten iron, etc., all affect graphitization and the microstructure of cast iron.
1. The influence of chemical composition
Among the common C, Si, Mn, P, and S in cast iron, C and Si are elements that strongly promote graphitization, and S is an element that strongly hinders graphitization. In fact, the influence of each element on the graphitization ability of cast iron is extremely complicated. Its influence is related to the content of each element itself and whether it interacts with other elements, such as Ti, Zr, B, Ce, Mg, etc., all hinder graphitization, but if its content is extremely low (such as B, Ce<0.01%, T< 0.08%), they show the effect of promoting graphitization.
2. The effect of cooling rate
Generally speaking, the cooling rate of castings tends to be slower, the more favorable it is for crystallization and transformation according to the state diagram of Fe-G stable system, and full graphitization; on the contrary, it is favorable for crystallization and transformation according to the state diagram of Fe-Fe3C metastable system. Finally obtained white iron. Especially in the graphitization at the eutectoid stage, since the temperature is low, the cooling rate increases, and the diffusion of atoms is difficult, it is generally difficult to fully progress the graphitization at the eutectoid stage.
The cooling rate of cast iron is a comprehensive factor, which is related to the pouring temperature, the thermal conductivity of the molding material and the wall thickness of the casting. And usually these factors have basically the same impact on the two stages.
Increasing the pouring temperature can delay the cooling rate of the casting, which promotes both the first stage of graphitization and the second stage of graphitization. Therefore, increasing the pouring temperature can pulverize graphite to a certain extent, and can also increase the eutectoid transformation.
3. The effect of overheating and high temperature standing of cast iron
Within a certain temperature range, increasing the overheating temperature of the molten iron and extending the high-temperature standing time will result in the refinement of the graphite-based structure in the cast iron and increase the strength of the cast iron. If the superheat is further increased, the nucleation ability of the cast iron will decrease, and the graphite morphology will be deteriorated, and even free cementite will appear, which will decrease the strength, so there is a’critical temperature’. The critical temperature mainly depends on the chemical composition of the molten iron and the cooling rate of the casting. It is generally believed that the critical temperature of ordinary gray cast iron is about 1500-1550 ℃, so it is always hoped that the iron tapping temperature is higher.
Please keep the source and address of this article for reprinting: The graphitization process of cast iron and the factors affecting the graphitization of cast iron
Minghe Die Casting Company are dedicated to manufacture and provide quality and high performance Casting Parts(metal die casting parts range mainly include Thin-Wall Die Casting,Hot Chamber Die Casting,Cold Chamber Die Casting),Round Service(Die Casting Service,Cnc Machining,Mold Making,Surface Treatment).Any custom Aluminum die casting, magnesium or Zamak/zinc die casting and other castings requirements are welcome to contact us.
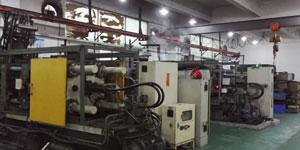
Under the control of ISO9001 and TS 16949,All processes are carried out through hundreds of advanced die casting machines, 5-axis machines, and other facilities, ranging from blasters to Ultra Sonic washing machines.Minghe not only has advanced equipment but also have professional team of experienced engineers,operators and inspectors to make the customer’s design come true.
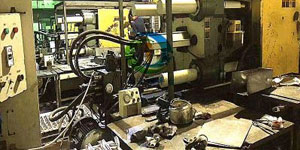
Contract manufacturer of die castings. Capabilities include cold chamber aluminum die casting parts from 0.15 lbs. to 6 lbs., quick change set up, and machining. Value-added services include polishing, vibrating, deburring, shot blasting, painting, plating, coating, assembly, and tooling. Materials worked with include alloys such as 360, 380, 383, and 413.
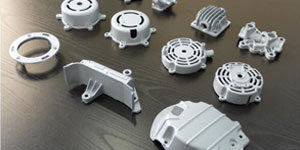
Zinc die casting design assistance/concurrent engineering services. Custom manufacturer of precision zinc die castings. Miniature castings, high pressure die castings, multi-slide mold castings, conventional mold castings, unit die and independent die castings and cavity sealed castings can be manufactured. Castings can be manufactured in lengths and widths up to 24 in. in +/-0.0005 in. tolerance.
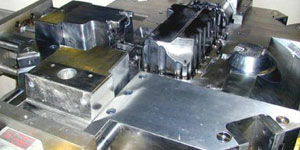
ISO 9001: 2015 certified manufacturer of die cast magnesium, Capabilities include high-pressure magnesium die casting up to 200 ton hot chamber & 3000 ton cold chamber, tooling design, polishing, molding, machining, powder & liquid painting, full QA with CMM capabilities, assembly, packaging & delivery.
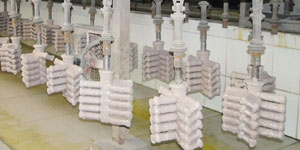
ITAF16949 certified. Additional Casting Service Include investment casting,sand casting,Gravity Casting, Lost Foam Casting,Centrifugal Casting,Vacuum Casting,Permanent Mold Casting,.Capabilities include EDI, engineering assistance, solid modeling and secondary processing.
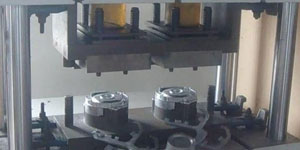
Casting Industries Parts Case Studies for: Cars, Bikes, Aircraft, Musical instruments, Watercraft, Optical devices, Sensors, Models, Electronic devices, Enclosures, Clocks, Machinery, Engines, Furniture, Jewelry, Jigs, Telecom, Lighting, Medical devices, Photographic devices, Robots, Sculptures, Sound equipment, Sporting equipment, Tooling, Toys and more.
What Can we help you do next?
∇ Go To Homepage For Die Casting China
→Casting Parts-Find out what we have done.
→Ralated Tips About Die Casting Services
By Minghe Die Casting Manufacturer |Categories: Helpful Articles |Material Tags: Aluminum Casting, Zinc Casting, Magnesium Casting, Titanium Casting, Stainless Steel Casting, Brass Casting,Bronze Casting,Casting Video,Company History,Aluminum Die Casting |Comments Off