I. Introduction
Due to changes in production conditions and the environment, other parameters of the casting will inevitably change. If the molding sand process cannot be adjusted in time, the sand system will be unstable, which will eventually lead to more difficult cleaning of the casting or even scrap;
In this way, it is necessary to adjust the original molding sand process to stabilize the sand system; the material composition of molding sand is mainly composed of old sand, raw sand, bentonite and additives. Since more than 95% of the molding sand is old sand, and the old sand is affected by factors such as the different sand-to-iron ratio of the casting and the different mixing amount of the core sand, resulting in very large fluctuations in the material composition. Therefore, to control the composition of molding sand, it is necessary to inspect the effective bentonite content, effective additive content and mud content in the molding sand in order to determine the added amount of bentonite, additives and raw sand during sand mixing.
This article will briefly introduce how the foundry of the author’s company is rooted in the actual production process.
According to the change of parameters, the molding sand process is adjusted to ensure the stability of the sand system.
2. Definition of key parameters of molding sand:
1. Effective bentonite content: The effective bentonite (active) content is determined based on the characteristics of the montmorillonite mineral contained in the bentonite that can absorb methylene blue and other dyes; it refers to the titration of 5.00g molding sand with 0.20% concentration reagent pure methylene blue solution [ mL]; converted according to the standard curve formula of bentonite (%)
2. Effective additive dosage: It is compared with the gas evolution of molding sand additives and calculated by using the formula; that is, the gas evolution of 1.00g molding sand at 900°C [mL] minus the gas evolution of the activated bentonite in the molding sand (the average amount measured before calculation ) Then compare with 1g additive gas volume (%).
3. Mud content: According to the national standard GB/T9442-1998, fine powder particles with a diameter less than 20μm are defined as mud. The sludge is usually removed by flushing method [2].
4. Molding sand particle size: expressed in AFS fineness, that is, the average size of sand particles is reflected according to the imaginary sieve mark [3];
5. AFS fineness calculation method: The AFS fineness measurement procedures and calculation methods specified by the American Institute of Foundry are as follows:
①. First weigh about 50g of the sand sample to be measured, wash off the mud, dry, and then sieving
②. Weigh and record the quality of the sand particles remaining on each sieve;
③. Calculate the percentage of the amount of sand particles remaining on each sieve to the total amount of sand samples;
④. Multiply the percentage of the amount of sand particles remaining on each sieve by the “AFS fineness multiplier” corresponding to each sieve;
⑤. Add the above products for each sieve number to find the sum:
⑥. Divide the sum obtained in item 5 by the sum of the percentages of retained sand on each sieve in item 3 to obtain the AFS fineness
3. Adjustment plan:
The sand mixing equipment used by the factory is DISA sand mill and molding equipment KW static pressure molding line; using data statistics for half a year, the following plans have been formulated for its molding sand system:
1. Statistics:
① Determine the amount of molding sand added to each box according to the setting value of the molding host, and calculate the sand-to-iron ratio of each box of castings according to the weight of each box of castings and the weight of the pouring system, and the amount of core sand used in the casting;
②Statistics on the amount of waste sand discharged and the usage of core sand and auxiliary materials
③ Statistics of dust removal of molding sand system
2. Sand adjustment:
① According to the production situation, when a casting is continuously produced for two or more days, the added amount of molding sand accessories (bentonite, additives) shall be fixed, and the changes in the effective amount of molding sand shall be counted, and then gradually verified during the continuous production of other castings The relationship between sand to iron ratio and added amount;
② Adjustment of molding sand particle size: adjust according to the median value of 50/100 sieve (silica sand of 50/100 sieve, the median value of the average fineness is 50 [4]), when the AFS of the molding sand is less than or equal to 50, by adding fine sand 70/140 or finer new sand 140/70 is adjusted, 30kg-60kg is added per mill, and the change in particle size is analyzed.
③ Adjustment of the mud content of molding sand: analyze the change of mud content of the molding sand system through the statistics of the daily dust removal;
Fourth, the specific adjustment process:
1. Statistics of casting sand to iron ratio:
(Note: Since the X2B1 cylinder body is cast with integral sand core, it will not burn the molding sand, so the weight of the outer molding sand of the casting is calculated as “0”)
2. Adjust the effective amount according to the sand-to-iron ratio of the casting. The sand-to-iron ratio of the 56D cylinder block is 6.57. Among the above castings, the sand-to-iron ratio is the highest among the cylinder block castings. Therefore, the 56D cylinder block is first tested:
When 56D was produced for three consecutive days, the additive amount was 22kg/mill, and the clay additive amount was 33kg/mill; the effective amount of additives rose from 4.55% to 5.03%; the effective amount of clay rose from 6.56% to 7%; an increase of about 0.5 %; It means that when 56D cylinder is produced, the added amount should be adjusted to be higher than the balance value of the sand system;
Through the above data analysis, the amount of auxiliary materials added is adjusted as follows:
1) When the cylinder is reproduced, the additive amount is adjusted to 19kg/mill, and when the clay additive amount is 26kg/mill, data statistics for three consecutive days show that the effective amount of additives has changed from 4.36% to 4.29%; the effective amount of clay has changed from 4.36% to 4.29%. 7.22% becomes 7.11%; the effective amount fluctuates by 0.1%; therefore, the process adjustment plan is reasonable and can ensure the balance of the molding sand system;
2) Similarly, the relationship between the amount of auxiliary materials added to other castings and the effective amount is calculated through experimental data analysis and theory; when reproducing different castings, adjust the appropriate amount of auxiliary materials added.
3. Use 70/140 mesh new sand and 140/70 new sand to adjust the sand size (the mud content of the prototype sand is 11.42%):
① From January 16th to January 21st, a total of 4257 sand grinding times in five days, about 4257*3/900=14 times; the particle size of each cycle changes about 0.26 (per grinding); therefore, the molding sand on January 16 The AFS value is 49.15; from January 16th, five days of continuous addition of 70/140 new sand to adjust the particle size, 60kg per mill, the AFS value of the molding sand on January 21st is 52.84;
② From January 25th to January 27th, a total of 2165 sand grinding times in three days, approximately 2165*3/900=7 cycles; the grain size of each cycle changes approximately 0.22 (per grinding); therefore, January 24 sand AFS =52.44, when the particle size of the molding sand reaches 52-53, the continuous addition of 70/140 new sand has little effect on the sand system AFS; starting from January 26, 140/70 new sand is added for three consecutive days to adjust, and 60kg is added for each grinding, 1 On the 28th, the AFS of the sand is 54.
(Note: ①The FAW enterprise standard stipulates that the sieving rate of 70/140 quartz sand 70,100,140 ≥80%, of which 70,100 sieving ≥60%; 140/70 quartz sand 70,100,140 sieving rate ≥80%, of which 100,140 sieving rate ≥60% ②Each grinding volume is 3 tons, and the system sand volume is estimated to be 900 tons)
4. Comparison of mud content and dust removal for three consecutive months:
Due to the cold climate in the north from February to March, the dust in the cold dust removal pipeline will condense and solidify after the hot dust is removed. If the pipeline is not cleaned in time, blockages will occur frequently, and the daily discharge will vary from 4 to 8 tons. The mud content of the sand system fluctuates greatly. During this period, the only way to increase the dust removal capacity and reduce the mud content is by increasing the air volume of the dust removal equipment and dredging the pipes;
After entering April, the temperature gradually increased, the phenomenon of dust condensation and solidification no longer appeared, the amount of dust removal gradually stabilized, reaching an average discharge of 7-8 tons per day, and the fluctuation range of mud content was reduced;
The mud content of the molding sand system can also be reduced by adding new sand or reducing the addition of auxiliary materials. The disadvantages of these two methods will be explained in the test conclusion.
5. Test conclusion
1. Adjust the effective amount of sand accessories
The bentonite crystals are damaged to a certain extent by heating, and the wet bonding strength will obviously decrease after adding water and mixing. After heating at higher temperature and longer time, the crystal structure of bentonite is completely destroyed, and it becomes “dead clay” with no cohesive force. Increased casting thickness, low sand-to-iron ratio, high pouring temperature and long cooling time all increase the burning loss of bentonite.
The most direct way to judge whether the effective coal powder in the molding sand is sufficient is to observe the smoothness of the surface of the casting and whether there is sand sticking. Part of the coal in the old sand is burned due to the heat of the poured molten metal and needs to be replenished. On the other hand, newly added materials such as fresh sand, mixed core sand and bentonite also need to be added to achieve the level of effective pulverized coal. The total amount of pulverized coal added during sand mixing is the sum of the burning loss and the additional supplementary amount. (Effective coal powder is equivalent to the effective additive in the text)
2. Adjustment of sand size:
The particle size of high-pressure molding sand is generally 50/140, while the particle size of resin sand cores is mostly 50/100 or coarser. Excessive mixing of core sand will affect the coarsening of the entire old wet sand, which will increase the permeability of the sand and rough the surface of the casting.
In order to keep the particle size of the molding sand from becoming coarse, the particles from the dust removal system can be recycled into the old sand. Or add fine new sand to adjust; as mentioned in the foundry, when the AFS of the molding sand reaches about 48, adjust by continuously adding 70/140 or 140/70 new sand; however, because the castings are broken into the core of the sand system The amount of sand is already large. If the particle size of the molding sand is not coarsened to an unbearable degree, it is not recommended to add such a large amount of new sand continuously, otherwise it will affect other performance indicators of the molding sand system (mud content, effective amount and strength due to the excessive amount of new sand). )have influence on;
3. Adjustment of mud content
The increase of the mud content will cause the permeability of the molding sand to decrease, and the phenomenon of “gas explosion” will occur during the pouring process, and the casting will be scrapped due to the explosion and sticky sand. The mud content of the molding sand system should not be too high; the mud content of the sand system can be reduced by reducing the amount of auxiliary materials, but the reduction of the effective bentonite content will cause the strength of the molding sand to decrease, and the ability to lift and resist sand will be reduced; the effective dosage of Decrease will cause the sand anti-sticking ability of the molding sand to decrease.
If you increase the amount of new sand added to adjust the mud content, first calculate how much mud the various newly added materials produce in the cast sand, and then you can calculate how much raw sand needs to be added to make the mud content of the molding sand meet the process Regulations.
As mentioned in the article, the mud content can be reduced by 0.1% for every 30 kg of new sand added in the foundry; however, the excessive addition of new sand will not only cause a waste of costs, but also reduce the proportion of used sand in the molding sand system, which will reduce the performance of the molding sand. , The molding sand diverges, which affects the ability of the molding sand to mold, and the sand washing phenomenon occurs during the casting process;
Therefore, the author believes that it is the best choice if the mud content of the sand system can be controlled by adjusting the dust removal equipment.
All in all, the stabilized sand system is to be able to produce high-quality castings. Through this concept, we must continuously adjust the molding sand process according to changing production conditions to meet production needs.
Please keep the source and address of this article for reprinting: How to ensure the stability of the green sand system?
Minghe Die Casting Company are dedicated to manufacture and provide quality and high performance Casting Parts(metal die casting parts range mainly include Thin-Wall Die Casting,Hot Chamber Die Casting,Cold Chamber Die Casting),Round Service(Die Casting Service,Cnc Machining,Mold Making,Surface Treatment).Any custom Aluminum die casting, magnesium or Zamak/zinc die casting and other castings requirements are welcome to contact us.
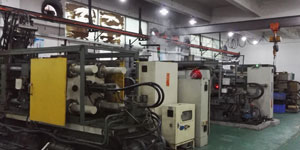
Under the control of ISO9001 and TS 16949,All processes are carried out through hundreds of advanced die casting machines, 5-axis machines, and other facilities, ranging from blasters to Ultra Sonic washing machines.Minghe not only has advanced equipment but also have professional team of experienced engineers,operators and inspectors to make the customer’s design come true.
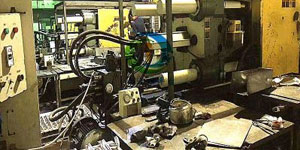
Contract manufacturer of die castings. Capabilities include cold chamber aluminum die casting parts from 0.15 lbs. to 6 lbs., quick change set up, and machining. Value-added services include polishing, vibrating, deburring, shot blasting, painting, plating, coating, assembly, and tooling. Materials worked with include alloys such as 360, 380, 383, and 413.
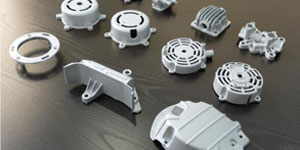
Zinc die casting design assistance/concurrent engineering services. Custom manufacturer of precision zinc die castings. Miniature castings, high pressure die castings, multi-slide mold castings, conventional mold castings, unit die and independent die castings and cavity sealed castings can be manufactured. Castings can be manufactured in lengths and widths up to 24 in. in +/-0.0005 in. tolerance.
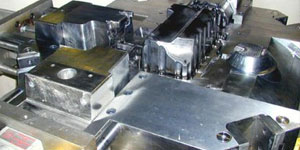
ISO 9001: 2015 certified manufacturer of die cast magnesium, Capabilities include high-pressure magnesium die casting up to 200 ton hot chamber & 3000 ton cold chamber, tooling design, polishing, molding, machining, powder & liquid painting, full QA with CMM capabilities, assembly, packaging & delivery.
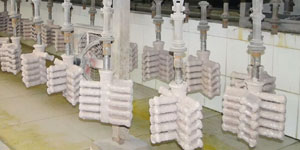
ITAF16949 certified. Additional Casting Service Include investment casting,sand casting,Gravity Casting, Lost Foam Casting,Centrifugal Casting,Vacuum Casting,Permanent Mold Casting,.Capabilities include EDI, engineering assistance, solid modeling and secondary processing.
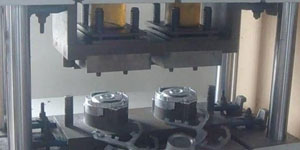
Casting Industries Parts Case Studies for: Cars, Bikes, Aircraft, Musical instruments, Watercraft, Optical devices, Sensors, Models, Electronic devices, Enclosures, Clocks, Machinery, Engines, Furniture, Jewelry, Jigs, Telecom, Lighting, Medical devices, Photographic devices, Robots, Sculptures, Sound equipment, Sporting equipment, Tooling, Toys and more.
What Can we help you do next?
∇ Go To Homepage For Die Casting China
→Casting Parts-Find out what we have done.
→Ralated Tips About Die Casting Services
By Minghe Die Casting Manufacturer |Categories: Helpful Articles |Material Tags: Aluminum Casting, Zinc Casting, Magnesium Casting, Titanium Casting, Stainless Steel Casting, Brass Casting,Bronze Casting,Casting Video,Company History,Aluminum Die Casting |Comments Off